CMC500u 5-Axis Vertical Machining Center
General layout of machine
The CMC650u five-axis machining center adopts a five-axis frame layout. The column and the bed are integrated. The ram moves up and down along the slide (Z direction), the slide-rest moves longitudinally along the slide (Y direction), and the slide moves laterally along the column (X),-60°~+110°tilted rotation of turntable along Y axis (B axis),Rotary motion of table surface 360 °along Z axis (C axis).The large parts all adopt high strength MEEHANITE cast iron material,including bed,column,slider-rest, slider etc.. They are optimized by 3D computer software, reasonable arrangement of stiffened plates and complete heat treatment process to eliminate residual stress, ensuring the machine with sufficient strength, rigidity and high stability.
2.System
Equipped with Siemens 840D controller and drives, it’s with complete function and simple operation;standard is with communication interface, UF interface and relevant software, as well as DNC on-line processing function.
3.Drive system
X,Y adopt THK 45mm roller linear guide way, Z axis adopts THK 35mm roller linear guide way, which has small friction and wear, high positioning accuracy and sensitivity,small vibration on high speed,long service life, interchangeability, as well as excellent servo drive performance, improving machine accuracy and stability
X,Y,Z axis servo motors connect with Taiwan high precision ball screws directly by elastic coupling, realizing gap-free drive, flexible feed, accurate positioning and high transmission accuracy.
Z axis servo motor is with self braking function,in the case of power failure, it can brake automatically and hold the motor shaft tightly, offering safety protection.
B, C-axis servo motor direct drive transmission, reducing transmission error, achieving high-precision transmission, accurate positioning, high transmission accuracy.
4.Spindle
Spindle adopts Taiwan 12000rpm direct connection spindle with high precision and rigidity. P4 grade NSK bearing is used for spindle specially. The spindle is assembled under constant temperature and then pass through dynamic balance calibration and running test, improving the whole spindle’s service life and reliability.The high-precision oil cooler is equipped to cool the electric spindle unit, and the stepless speed regulation can be realized in the range of its speed. The spindle is controlled by the built-in encoder of the motor, which can realize the spindle orientation and rigid tapping function.
5.Tool magazine
The Taiwan disc type 24pcs tool magazine is installed on the side of the column. When the tool is changed, the magazine is driven and positioned by the roller cam mechanism. After the spindle reaches the tool change position, the tool changer (ATC) is used to complete the action of tool changing. ATC is a hobbing cam mechanism. After preloading, it can run at high speed and no noise, making the tool change process fast and accurate.
6.Cooling system
Large flow cooling pump and large volume water tank are equipped to ensure circulation cooling,power of cooling pump:840W,66.7L/min large flow cooling pump supplies the cooling fully.Spindle end is equipped with cooling nozzle, it can be either water cooling or air cooling, and can be switched at will. Air gun is equipped for cleaning the machine.
7.Pneumatic system
Pneumatic two-piece can filter the impurity and moisture in the air source and prevent the damage and corrosion of machine parts caused by impure gas.Electromagnetic valve is controller by PLC program which can make sure the actions can be finished quickly and correctly, such as spindle releasing the tool,spindle blowing,spindle clamping tool etc.
8.Machine guard
The machine guards conform to safety standard,not only prevents coolant splash, but also ensures safe operation,and the appearance is beautiful. Every guide way is equipped with protection cover which can prevent chips,coolant from damaging guide ways and ball screws.
9.Lubrication system
Guide ways and ball screws are all centralized auto lubrication,each node is equipped with a quantitative oil separator which will inject the oil to lubricating parts quantitatively and regularly ensuring uniform lubrication and effectively reducing friction resistance, movement accuracy is improved,the service life of ball screws and guide ways are ensured.
10.Chip removal system
The iron chips produced in the processing fall directly into the protective compartment. The internal slant structure of the protection allows the iron chips to slide smoothly into the chain type conveyor and collect the iron chips in the chip box through the chain plate.
11. Detection system
The machine is equipped with the British Renishaw contact tool setter TS-27R and the probe OMP60. Among them, TS-27R can perform tool setting and breakage detection; OMP60 can measure the machining accuracy of processed workpieces online.
12.Working condition
(1)Power supply:380V±10% 50HZ±1% three-phase alternating current
(2)Use Temperature:5℃-40℃
(3)Perfect environmental temperature:15℃-25℃
(4)Relative humidity:40-75%
(5)Air pressure:0.5-0.7Mpa
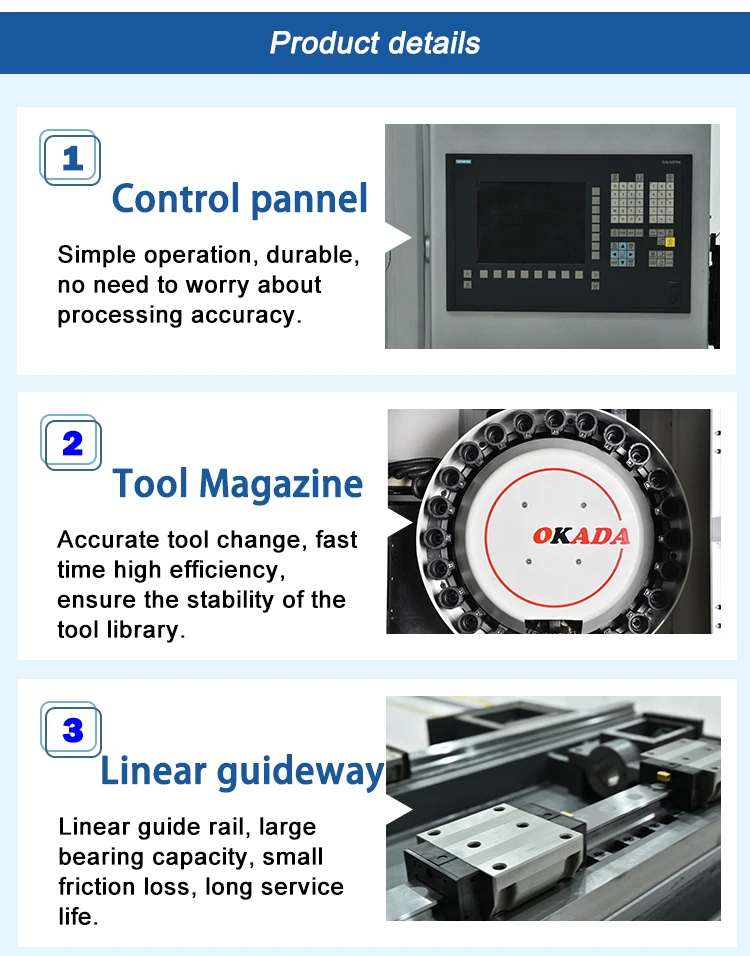
CMC500u 5-Axis Vertical Machining Center
|
unit
|
CMC500u
|
Table size
|
mm
|
φ650*540
|
Number/Width/Distance of T-slot
|
mm
|
5-14-100
|
Max. load of table
|
kg
|
300
|
Distance from spindle nose to table surface
|
mm
|
150-625
|
|
|
Distance from spindle axis to column guideway
|
|
190
|
Rapid feed speed
|
m / min
|
42
|
Feed speed
|
mm/min
|
2.5-10000
|
Taper of spindle
|
|
BT40
|
Spindle speed range
|
rpm
|
40-12000
|
Spindle motor power
|
kW
|
7.5
|
Tool magazine capability
|
qyt
|
24
|
Max. weight of tool
|
kg
|
8
|
Max. dimension of tool
|
mm
|
Φ150*300
|
Positioning accuracy
|
mm
|
±0.005/300 JIS
|
Repeat positioning accuracy
|
mm
|
±0.003/300 JIS
|
Overall dimension
|
mm
|
3970×3210×2800
|
Machine weight
|
kg
|
8500
|
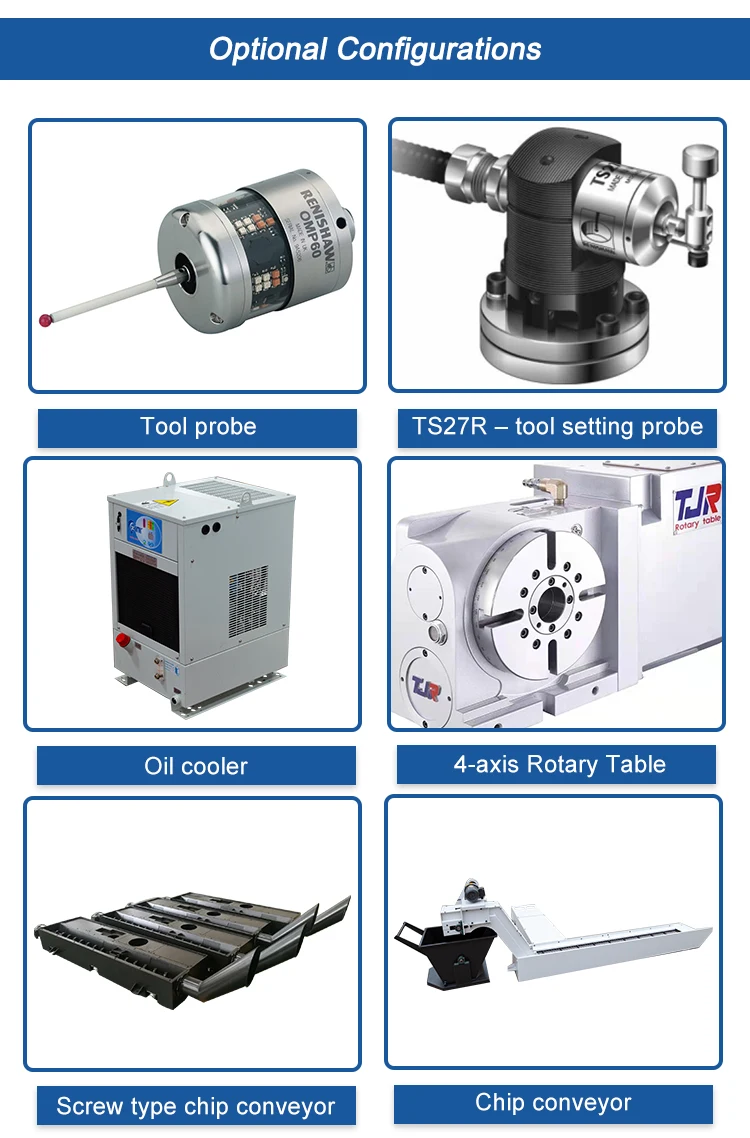
CMC500u 5-Axis Vertical Machining Center
General layout of machine
The CMC650u five-axis machining center adopts a five-axis frame layout. The column and the bed are integrated. The ram moves up and down along the slide (Z direction), the slide-rest moves longitudinally along the slide (Y direction), and the slide moves laterally along the column (X),-60°~+110°tilted rotation of turntable along Y axis (B axis),Rotary motion of table surface 360 °along Z axis (C axis).The large parts all adopt high strength MEEHANITE cast iron material,including bed,column,slider-rest, slider etc.. They are optimized by 3D computer software, reasonable arrangement of stiffened plates and complete heat treatment process to eliminate residual stress, ensuring the machine with sufficient strength, rigidity and high stability.
2.System
Equipped with Siemens 840D controller and drives, it’s with complete function and simple operation;standard is with communication interface, UF interface and relevant software, as well as DNC on-line processing function.
3.Drive system
X,Y adopt THK 45mm roller linear guide way, Z axis adopts THK 35mm roller linear guide way, which has small friction and wear, high positioning accuracy and sensitivity,small vibration on high speed,long service life, interchangeability, as well as excellent servo drive performance, improving machine accuracy and stability
X,Y,Z axis servo motors connect with Taiwan high precision ball screws directly by elastic coupling, realizing gap-free drive, flexible feed, accurate positioning and high transmission accuracy.
Z axis servo motor is with self braking function,in the case of power failure, it can brake automatically and hold the motor shaft tightly, offering safety protection.
B, C-axis servo motor direct drive transmission, reducing transmission error, achieving high-precision transmission, accurate positioning, high transmission accuracy.
4.Spindle
Spindle adopts Taiwan 12000rpm direct connection spindle with high precision and rigidity. P4 grade NSK bearing is used for spindle specially. The spindle is assembled under constant temperature and then pass through dynamic balance calibration and running test, improving the whole spindle’s service life and reliability.The high-precision oil cooler is equipped to cool the electric spindle unit, and the stepless speed regulation can be realized in the range of its speed. The spindle is controlled by the built-in encoder of the motor, which can realize the spindle orientation and rigid tapping function.
5.Tool magazine
The Taiwan disc type 24pcs tool magazine is installed on the side of the column. When the tool is changed, the magazine is driven and positioned by the roller cam mechanism. After the spindle reaches the tool change position, the tool changer (ATC) is used to complete the action of tool changing. ATC is a hobbing cam mechanism. After preloading, it can run at high speed and no noise, making the tool change process fast and accurate.
6.Cooling system
Large flow cooling pump and large volume water tank are equipped to ensure circulation cooling,power of cooling pump:840W,66.7L/min large flow cooling pump supplies the cooling fully.Spindle end is equipped with cooling nozzle, it can be either water cooling or air cooling, and can be switched at will. Air gun is equipped for cleaning the machine.
7.Pneumatic system
Pneumatic two-piece can filter the impurity and moisture in the air source and prevent the damage and corrosion of machine parts caused by impure gas.Electromagnetic valve is controller by PLC program which can make sure the actions can be finished quickly and correctly, such as spindle releasing the tool,spindle blowing,spindle clamping tool etc.
8.Machine guard
The machine guards conform to safety standard,not only prevents coolant splash, but also ensures safe operation,and the appearance is beautiful. Every guide way is equipped with protection cover which can prevent chips,coolant from damaging guide ways and ball screws.
9.Lubrication system
Guide ways and ball screws are all centralized auto lubrication,each node is equipped with a quantitative oil separator which will inject the oil to lubricating parts quantitatively and regularly ensuring uniform lubrication and effectively reducing friction resistance, movement accuracy is improved,the service life of ball screws and guide ways are ensured.
10.Chip removal system
The iron chips produced in the processing fall directly into the protective compartment. The internal slant structure of the protection allows the iron chips to slide smoothly into the chain type conveyor and collect the iron chips in the chip box through the chain plate.
11. Detection system
The machine is equipped with the British Renishaw contact tool setter TS-27R and the probe OMP60. Among them, TS-27R can perform tool setting and breakage detection; OMP60 can measure the machining accuracy of processed workpieces online.
12.Working condition
(1)Power supply:380V±10% 50HZ±1% three-phase alternating current
(2)Use Temperature:5℃-40℃
(3)Perfect environmental temperature:15℃-25℃
(4)Relative humidity:40-75%
(5)Air pressure:0.5-0.7Mpa
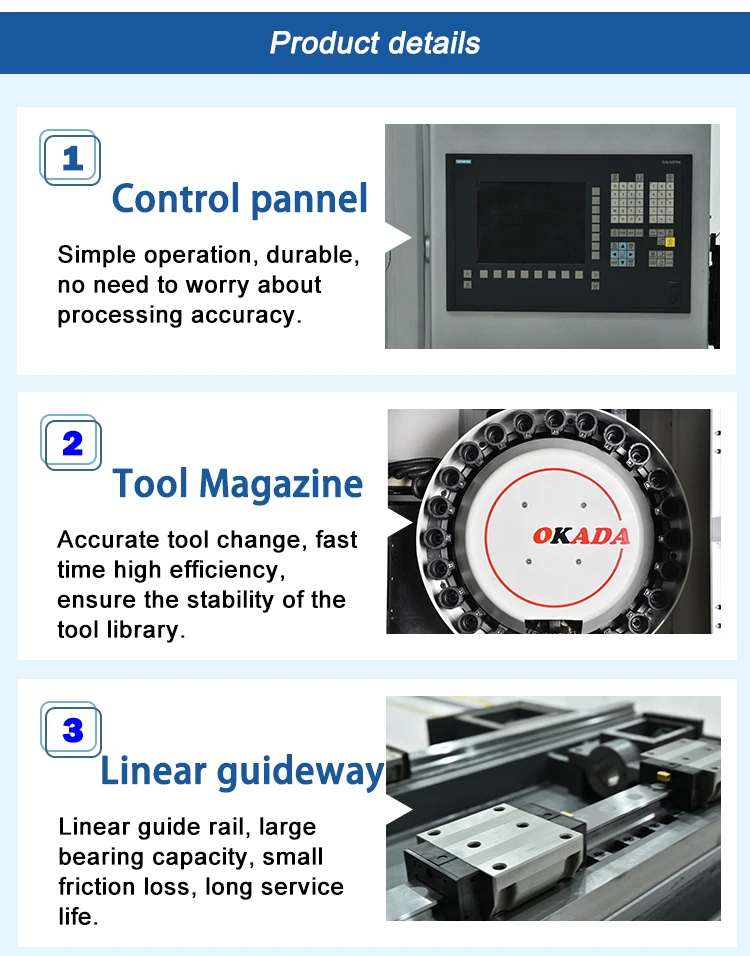
CMC500u 5-Axis Vertical Machining Center
|
unit
|
CMC500u
|
Table size
|
mm
|
φ650*540
|
Number/Width/Distance of T-slot
|
mm
|
5-14-100
|
Max. load of table
|
kg
|
300
|
Distance from spindle nose to table surface
|
mm
|
150-625
|
|
|
Distance from spindle axis to column guideway
|
|
190
|
Rapid feed speed
|
m / min
|
42
|
Feed speed
|
mm/min
|
2.5-10000
|
Taper of spindle
|
|
BT40
|
Spindle speed range
|
rpm
|
40-12000
|
Spindle motor power
|
kW
|
7.5
|
Tool magazine capability
|
qyt
|
24
|
Max. weight of tool
|
kg
|
8
|
Max. dimension of tool
|
mm
|
Φ150*300
|
Positioning accuracy
|
mm
|
±0.005/300 JIS
|
Repeat positioning accuracy
|
mm
|
±0.003/300 JIS
|
Overall dimension
|
mm
|
3970×3210×2800
|
Machine weight
|
kg
|
8500
|
|