TP35 TP45 Series Parallel Double Spindle Turning Center
Machine Characteristics
The TP34 TP45 series is an ultra-small parallel dual-spindle dual-turret turning center launched ; it can realize a complete processing solution integrating self-loading, compound multi-process processing, blanking, and inspection.
High-precision spindle system
1. High-precision and high-rigidity electric spindle.
2. Excellent processing efficiency (maximum speed up to 6000rpm).
3. Excellent precision performance (end face and internal and external cone runout ≤ 0.001mm).
Tool system
1.Double high rigidity and high torque power turrets.
2. High-speed powered tool holder greatly improves milling efficiency.
2. Dual power turret completes turning, milling and drilling processing more efficiently.
High rigidity saddle design
1.HT300 high strength casting, one year natural aging treatment.
2. Large-span ladder rail structure, high rigidity and high stability.
Applications
1. Shaft components: CNC lathes are capable of machining a range of shaft components such as transmission shafts, drive shafts,and crankshafts with high precision and efficiency.
2. Valve components: CNC lathes have the ability to machine valve components such as valve bodies, valve stems, and valve seats with high precision and tight tolerances.
3. Aerospace components: CNC lathes can be used to machine complex aerospace components such as engine components, landing gear components, and flight control components.
4. Electrical components: CNC lathes can be used to machine electrical components such as connectors, terminals, and conductive components with high accuracy and quality.
5. Medical components: CNC lathes can be used to create precise medical components such as surgical instruments, dental implants, and prosthetics.
6. Automotive components: CNC lathes are widely used in the automotive industry to manufacture components such as bearings,axles, and gears.
7. Hydraulic components: CNC lathes are capable of producing high-precision hydraulic components such as cylinders, pistons, and pump parts.
8. Mold components: CNC lathes are commonly used to produce mold components such as core pins, ejector pins, and cavity inserts with precision and efficiency.
9. Precision gears: CNC lathes are ideal for manufacturing precision gears such as spur gears, helical gears, and bevel gears with high accuracy and repeatability.
10. Sports equipment components: CNC lathes can be used to manufacture a variety of sports equipment components such as golf club heads, bicycle parts, and fishing reels.
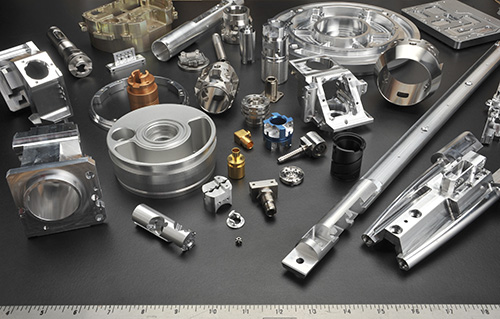
TP35 TP45 Series Parallel Double Spindle Turning Center
model
|
TP35Series
|
TP45Series
|
Spindle taper (main/auxiliary)(jis)
|
A2-5/A2-5
|
A2-6/A2-6
|
Standard chuck size (main/auxiliary)
|
6/6
|
8/8
|
Max spindle speed (main/auxiliary)(rpm)
|
6000/6000
|
4500/4500
|
Spindle power (main/auxiliary)(kw)
|
11/11
|
15/15
|
Max processing diameter(mm)
|
Φ250
|
Φ300
|
Max processing length(mm)
|
200
|
250
|
Number of tools12/15(pcs)
|
12/15
|
12/15
|
Tool specifications(mm)
|
25/Φ32
|
25/Φ40
|
Powered tool holder specifications
|
BMT45
|
BMT55
|
TP35 TP45 Series Parallel Double Spindle Turning Center
Optional: Tailstock system
1. The unique roof seat system is optional to make up for the shortcomings and is not afraid of processing slender shafts.
2.NC intelligent tailstock, programmable control of thrust, speed and position.
3. Simple rotating tailstock with excellent rigidity and precision.
Optional: Y-axis system
1. Optional Y-axis system: modular design.
2. Achieve more powerful turning, milling and grinding multi-process composite processing.
TP35 TP45 Series Parallel Double Spindle Turning Center
Machine Characteristics
The TP34 TP45 series is an ultra-small parallel dual-spindle dual-turret turning center launched ; it can realize a complete processing solution integrating self-loading, compound multi-process processing, blanking, and inspection.
High-precision spindle system
1. High-precision and high-rigidity electric spindle.
2. Excellent processing efficiency (maximum speed up to 6000rpm).
3. Excellent precision performance (end face and internal and external cone runout ≤ 0.001mm).
Tool system
1.Double high rigidity and high torque power turrets.
2. High-speed powered tool holder greatly improves milling efficiency.
2. Dual power turret completes turning, milling and drilling processing more efficiently.
High rigidity saddle design
1.HT300 high strength casting, one year natural aging treatment.
2. Large-span ladder rail structure, high rigidity and high stability.
Applications
1. Shaft components: CNC lathes are capable of machining a range of shaft components such as transmission shafts, drive shafts,and crankshafts with high precision and efficiency.
2. Valve components: CNC lathes have the ability to machine valve components such as valve bodies, valve stems, and valve seats with high precision and tight tolerances.
3. Aerospace components: CNC lathes can be used to machine complex aerospace components such as engine components, landing gear components, and flight control components.
4. Electrical components: CNC lathes can be used to machine electrical components such as connectors, terminals, and conductive components with high accuracy and quality.
5. Medical components: CNC lathes can be used to create precise medical components such as surgical instruments, dental implants, and prosthetics.
6. Automotive components: CNC lathes are widely used in the automotive industry to manufacture components such as bearings,axles, and gears.
7. Hydraulic components: CNC lathes are capable of producing high-precision hydraulic components such as cylinders, pistons, and pump parts.
8. Mold components: CNC lathes are commonly used to produce mold components such as core pins, ejector pins, and cavity inserts with precision and efficiency.
9. Precision gears: CNC lathes are ideal for manufacturing precision gears such as spur gears, helical gears, and bevel gears with high accuracy and repeatability.
10. Sports equipment components: CNC lathes can be used to manufacture a variety of sports equipment components such as golf club heads, bicycle parts, and fishing reels.
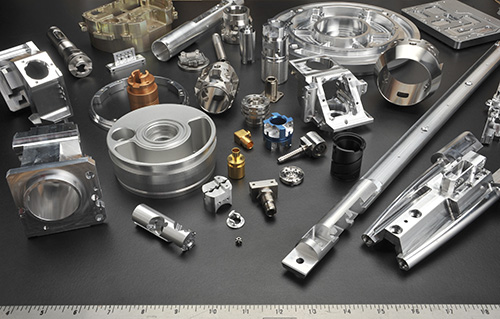
TP35 TP45 Series Parallel Double Spindle Turning Center
model
|
TP35Series
|
TP45Series
|
Spindle taper (main/auxiliary)(jis)
|
A2-5/A2-5
|
A2-6/A2-6
|
Standard chuck size (main/auxiliary)
|
6/6
|
8/8
|
Max spindle speed (main/auxiliary)(rpm)
|
6000/6000
|
4500/4500
|
Spindle power (main/auxiliary)(kw)
|
11/11
|
15/15
|
Max processing diameter(mm)
|
Φ250
|
Φ300
|
Max processing length(mm)
|
200
|
250
|
Number of tools12/15(pcs)
|
12/15
|
12/15
|
Tool specifications(mm)
|
25/Φ32
|
25/Φ40
|
Powered tool holder specifications
|
BMT45
|
BMT55
|
TP35 TP45 Series Parallel Double Spindle Turning Center
Optional: Tailstock system
1. The unique roof seat system is optional to make up for the shortcomings and is not afraid of processing slender shafts.
2.NC intelligent tailstock, programmable control of thrust, speed and position.
3. Simple rotating tailstock with excellent rigidity and precision.
Optional: Y-axis system
1. Optional Y-axis system: modular design.
2. Achieve more powerful turning, milling and grinding multi-process composite processing.
|